Discolouration of Watch Dials
Why it happens and how it can be controlled
22nd October, 2020
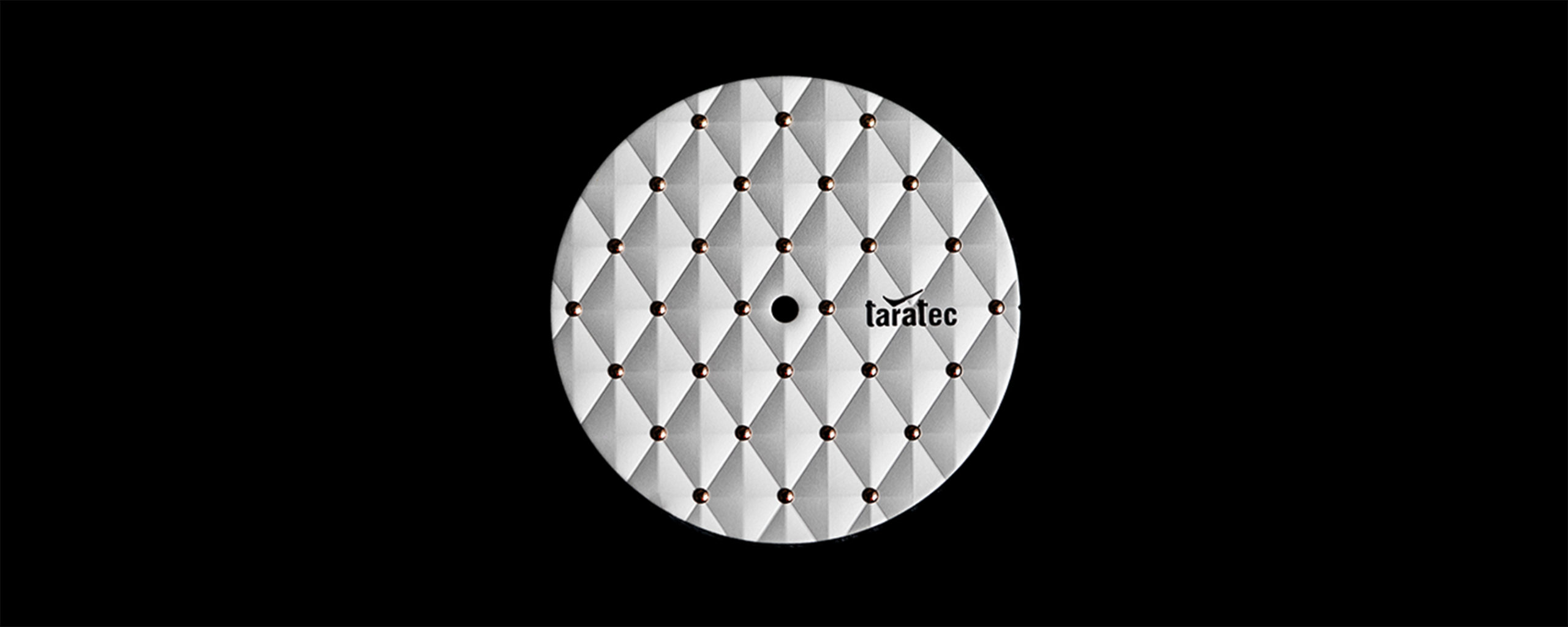
Among usual wear and tear, watches are often prone to discolouration. And in general, the older the watches, the more prone they are to fading or discolouration. The components that are most susceptible are the dials and hands. The watch case and bezels may also be subject to discolouration, but this is rare unless they are gold-plated and/or PVD coated. This article deals with some of the causes of discolouration of dials; a supplement will cover other causes that may negatively impact dials and hands.
The most common cause of discolouration is sunlight, specifically the Ultraviolet (UV) rays that form a part of sunlight. There are three main types of UV rays: UVA, UVB and UVC representing three different wavelengths sizes. Most of the UVC -representing the smallest wavelengths,from 100 to 280nm- do not reach the earth’s surface since they are absorbed by our planet’s atmosphere and ozone layer. UVB rays, measuring in the range of 280-315 nm are of medium wavelength. Some UVB are absorbed by the atmosphere, while a portion reaches us on the ground. UVA is the largest wavelength of ultraviolet. The bulk of UV rays that reach the Earth are UVA, measuring between 315-380nm. Together the UVA and UVB that hit the earth’s surface can cause significant alterations to the visual aspect of coloured materials. It is impossible to avoid exposure to sunlight. And even if exposure to direct sunlight is minimised, UV rays will still be present. But what exactly is discolouration? Well, UV rays are known to discolour the pigments and resin that are part of the varnish or lacquer used to overcoat all dials.
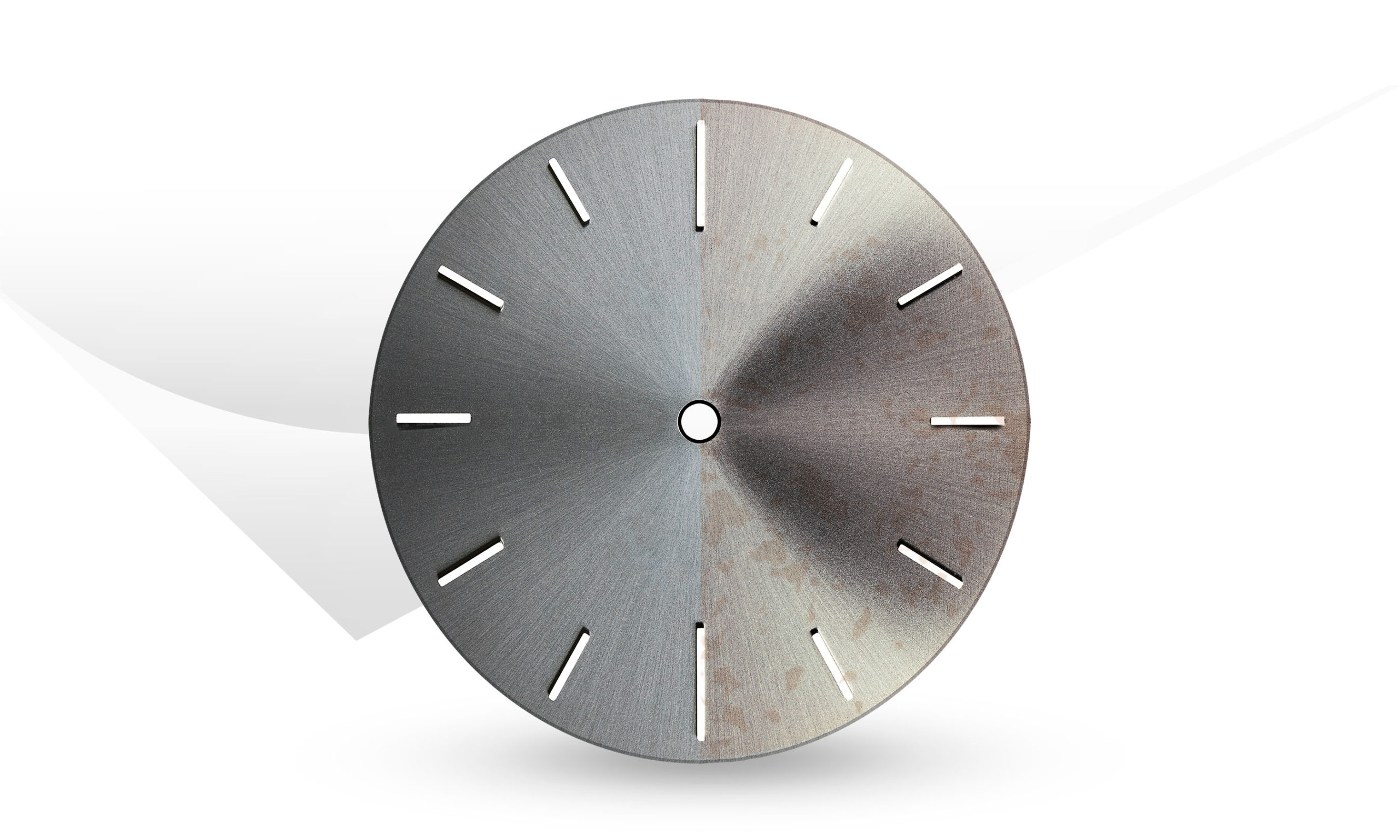
Original (Left) and Discoloured (Right)
Dials with metallic finishes and colours, are plated with silver, gold, nickel or palladium. Typically, such dials are over-coated with a clear varnish to protect the metal plating and also to make them stain-resistant. The varnish must be water clear to preserve the natural colour of the metal. But with exposure to UV rays, the resin in the varnish tends to become yellowish –this is often seen on old watches with silver coloured dials. UV light also breaks down the bonds in colour pigments and causes fading. So dials coated with paint can also discolour over time.
At the Taratec dials factory, we conduct the sunlight test on all the batches to ensure that they are optimally protected from fading. We run this state-of-the-art test to simulate long sunlight exposure on samples from every lot of dials we produce. This is commonly known as the SUNLIGHT test.
We at Taratec are very particular about the quality of paints and varnishes used. They are sourced from specialised manufacturers who engineer them to be UV resistant and are certified as such. The storage conditions of the lacquers and varnishes, during transportation and in our workshops is also very important. For instance, exposure to high temperatures can cause damage so if they are to be transported over long distances, it is done by air, and storage is carried out in a cool temperature-controlled setting. Next is the quality of application –inappropriate methods of coating can leave the underlying metal coat exposed and allow staining.
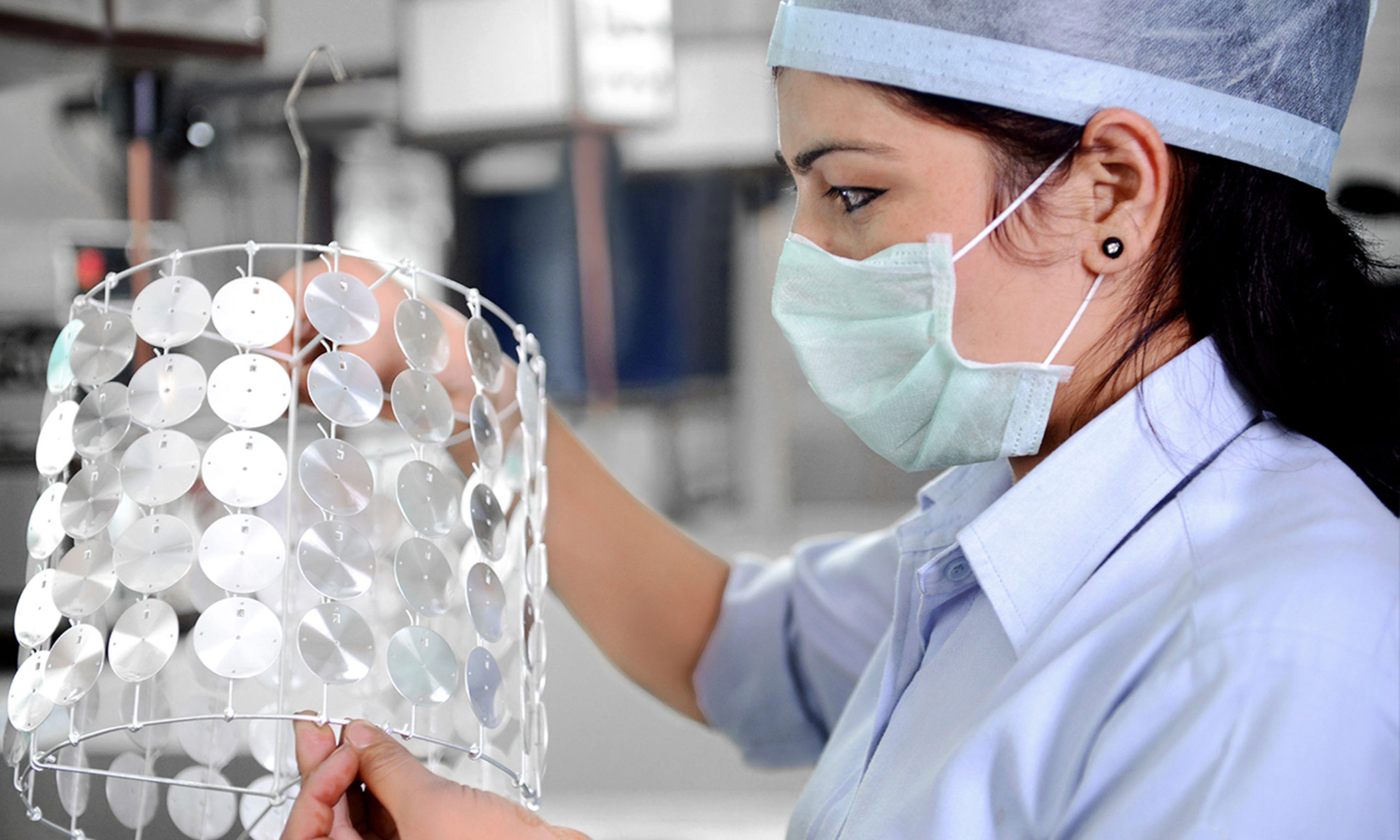
The Sunlight Test is a complex stage-by-stage process and takes into account all the guidelines set by the NIHS (Norme de l’Industrie Horlogère Suisse), which recommends testing for a minimum of 36 hours. The test starts with placing a watch dial in a test chamber with one ormore filtered light sources. A Xenon Arc lamp or a metallic halide lamp is employed to control the irradiance levels in the chamber, which are maintained between 290 – 400 nm at all times.The humidity levels are fixed at 60% and the temperature at 65° Celsius (a standard black thermometer is used to ensure there are no discrepancies). Once the dial has spent 72 hours inside the chamber, it is taken out, laid out flat on a specimen holder and visually inspected by askilled expert for signs of discolouration. Attention to detail is vital. Here, for example, we ensure that the dial being tested is half-covered in foil, in order to have a reference point when it comes to making a conclusive analysis on whether it has passed the test or not. If even the minutest trace of discolouration is detected on the tested part as compared to the unexposed area, the sample is immediately rejected. This test is designed to be very rigorous meeting the highest standards of excellence specified by NIHS.
The outcome? Dials which go on to become part of the best-engineered watches in the world and craftsmanship we have the privilege of encountering in the world of watches. Taratec is one of few dial makers who test components under extreme conditions. The SUNLIGHT TEST is one example.