HOW WE MANUFACTURE
WORLD-CLASS, SHOCK-RESISTANT WATCH DIALS
Going above and beyond in processes as well as testing
2nd February, 2021
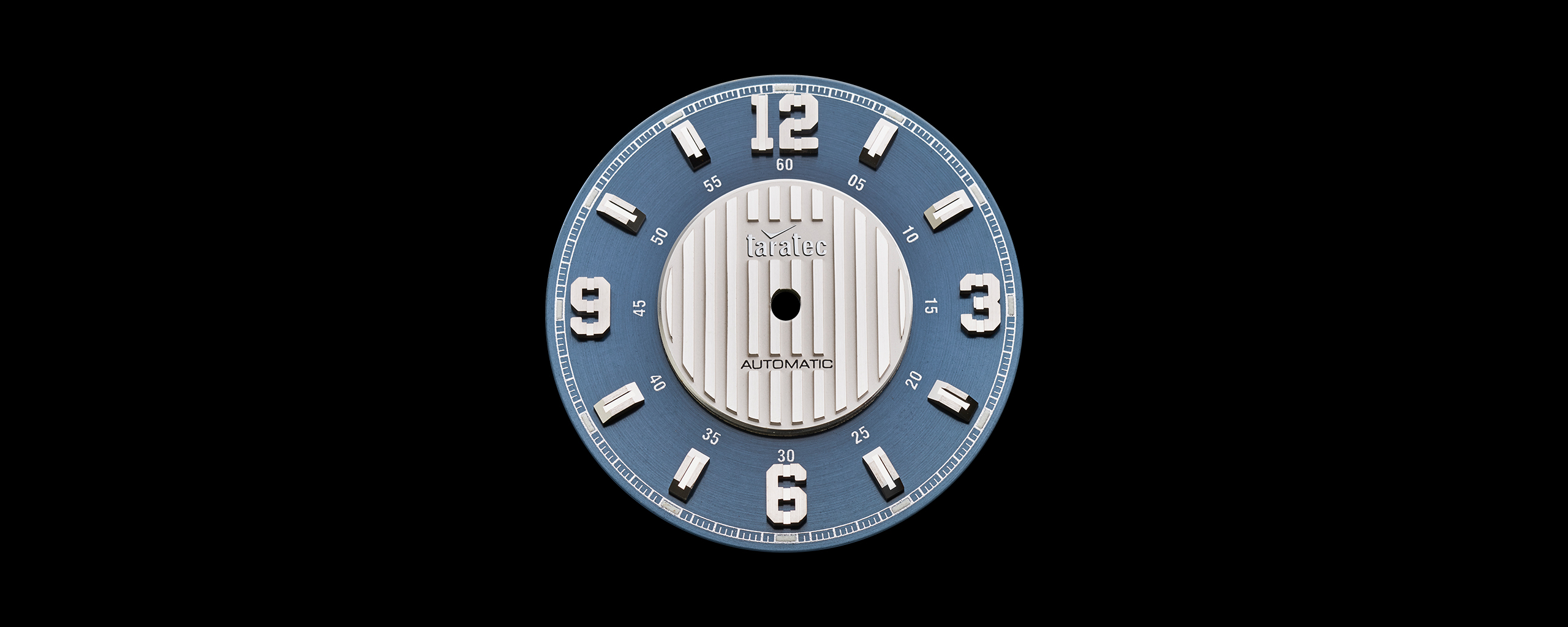
Ever since watches made their way from pockets to wrists, their use and application in demanding physical situations has only increased. While this evolution began in the early 20th century, it was soon discovered that a consequence of this more rugged usage of wristwatches was them being subjected to many different shocks. Whether they are accidental, direct, in-use, due to a fall, motion of hands or sudden jerks – there are just so many ways in which a watch can undergo shock.
Traditional remedies to this problem looked at preserving the most delicate parts of the movement (i.e. the balance staff), so that timekeeping remained unaffected. This also led to some landmark innovations in the sphere of horology like the Incabloc shock protection system.
However, in order for the watch, as a whole, to live up to its warranted standards of robustness and performance, it is absolutely imperative for each component to effectively withstand shocks as well. Therefore, the dial, with its appliqués, indexes and luminescent portions cannot be left out of this conversation.
This is especially true when you consider how important sports, adventure and active lifestyles are, to the nature of communications watch brands engage in with their customers. Watch buyers today are more keen than ever to push their watches to the limit, taking into account the implicit level of engineering expected of any prestigious brand.
Recent Post
- Discolouration of Watch Dials 22nd October, 2020

Affected Dial
As suppliers to some of the most storied watch manufacturers in the world, we understand this responsibility. This is why our dial manufacturing and testing procedures go above and beyond, in order to meet your most stringent requirements and assurances to your customers.
At Taratec, we’re proud to say that we achieve class-leading shock resistance for our dials. We do this primarily through precise riveting processes which mechanically reinforce our applied dial components, in addition to traditional gluing methods. Furthermore, we carefully verify performance by carrying out the Drop Test or Pendulum Test in compliance with ISO 1413:2016 standards. This two-level procedure is testament to our quality commitments, placing us in a rare category of manufacturers that hold-up to the highest, internationally recognised levels of testing and scrutiny.
Let’s look at these in some more detail.
Careful craftsmanship reflected in our riveting process
The first step to achieving more robust shock-resistance for dials is ensuring that dial components have an added layer of mechanical security, instead of using just glue or adhesives. This increases longevity of the timepiece in much the same way that mechanical components in a watch movements do, when compared with circuit-driven timepieces.
Many manufacturers of watch dials prefer to use only glue while undertaking dial assembly. This is because it’s faster, easier, less technically demanding, as well as simpler to correct while assembling; allowing for higher tolerances.
While this serves certain customer applications well, for others, it results in a lower level of strength and solidity than what can practicably be achieved for that particular type of watch dial.
In addition to manufacturing dials with glued components, the craftsmen at Taratec are skilled and equipped to go one step further by riveting the indexes (and other applied components) to the dial. This process involves using indexes with cylindrical feet, which can be merged with the dial using specialised machinery and tools. The bond thus formed between the two parts is far stronger than the result achieved by using only glue.
The dual-stage procedure of gluing and riveting, however, involves checks and controls over a number of small, but important details. Illustratively, some of these are:
Applying the right amount of glue
Choosing the correct type and shape of the grinding tool
Using rotary machines at precise and appropriate speeds
Flaring the index feet for tougher bonds with the dial
Removing any remaining feet from the dial
Providing final outcomes that are free from any blemishes or micro-scratches
After a thorough visual inspection, dial samples are subjected to tests prescribed under the ISO 1413:2016 standard, which deals with shock-resistant wristwatches.
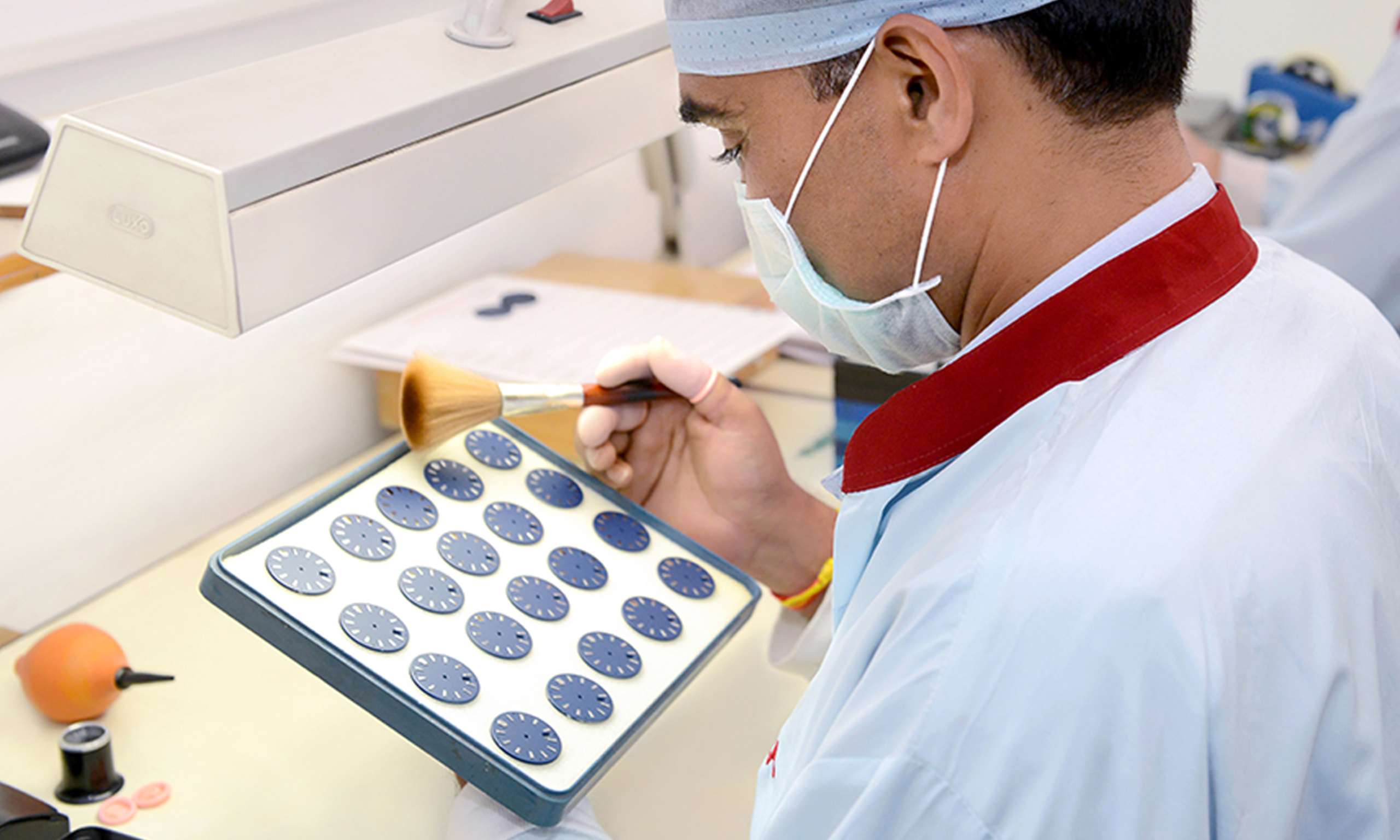
Testing that conforms to global standards
The ISO 1413:2016 standard prescribes criteria and minimum requirements that a cased watch needs to pass in order to earn the designation of a shock-resistant wristwatch. It offers two testing methods for the same – the Drop Test and the Pendulum Test – both of which simulate mechanical shocks that a watch may receive in use, but in different ways.
The Drop Test involves dropping the watch from a height of 1 metre onto a flat floor. This is why it is the most commonly used testing method in the watch component manufacturing industry. Taratec also carries out this test on dial samples after casing them. The specimen is dropped from a height of 1 metre onto a steel plate with a 1.5mm thick polyurethane layer, having a hardness of 90 Shore. The Drop Tests are done in three positions – impact on the glass, impact on the case back and impact at the 9hr position.
The Pendulum Test (inspired by the high-strain rate Charpy Impact Test), on the other hand, involves a specialised setup wherein a pendulum of known mass and length is dropped from a known height to impact the watch case. Taratec is among a handful of world-class dial manufacturers to have in-house capabilities for carrying out the Pendulum Test.
We carry out the Pendulum Test at room temperature after casing the dial and affixing the glass. This specimen is hit with a 3kg pendulum from a 1 metre distance, with an impact velocity of 4.43 m/s. This delivers approximately 30 Joules of energy to the specimen. We do this at three different positions, in compliance with ISO1413:2016 – impact on the glass, impact at the 9hr position of the watch case, impact on the watch crown.
After carrying out our tests, the dial is inspected and verified for any aesthetic or dimensional damage that may have taken place. We carefully inspect to see if all applied parts (indexes, rings, window frames, diamonds in bushing, or any other) have resisted the shock, and remain unaffected by it visually as well as structurally. Any aberration whatsoever results in rejection; our testing is rigorous and stringent.
Whether it is for your internal quality checks, homologation or receiving the ISO certification, Taratec is pleased to offer you the assurance of our dials passing shock-resistance tests prescribed by the most well-regarded global standards.
This commitment to being at the forefront of quality and technology is what makes us a trusted partner to some of the most aspirational luxury watch brands in the world. We like to push the boundaries of accepted industry-standards, and use our technical craftsmanship as well as expertise to manufacture complex dials and precision components that will last a lifetime.